PNEUMATIC ROBOTIC ARMS - CAPSTONE
This is my senior capstone project. Our goal was to create a pair of pneumatic robotic arms that could be remotely controlled. I worked in a group of six people and we each worked on different parts of the project. I worked on the design of the hand (grabber) and the forearm. For the design of the arms we used soft pneumatic actuators and rigid 3D printed bone structure. The video above shows the grabber that we created picking up a plastic cup. For the hand design, we used knit textile bending actuators for the fingers and a 3D printed palm that split the incoming air-flow evenly to the three fingers.


The knit textile bending actuators work by sewing two fabrics together and inserting an inflatable bladder in between the two fabrics. This works because of the stretch properties of the two fabrics. In the left image above, Fabric 1 is an elastic fabric that stretches in one direction and Fabric 2 is an inelastic fabric that does not stretch at all. An inflatable bladder is inserted in between the fabrics and inflated with an air pump. As it is inflated, the one-way stretch elastic fabric expands while the inelastic fabric does not. Different types of motion can be achieved by varying the way the pieces of fabric are sewn together. For our purposes, we designed the actuators to bend as a finger would, as you can see in the right image above.

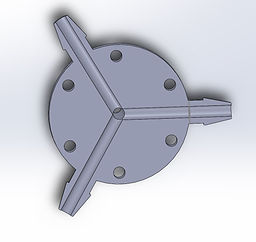
For the palm of the hand, we created a 3D printed air splitter that would evenly divide the incoming air from the pump to the three fingers. My partner created the initial design and I modified it later when designing the forearm. The images above show the initial design.


For the forearm, we decided to use pneumatic artificial muscles as the actuators and a 3D printed bone structure. We used pneumatic artificial muscles because they are great for linear actuation. This closely mimics the muscles that we have in our forearms. The actuators are constructed by inserting a balloon inside a mesh sleeve and sealing one end shut; the other end is connected to a tube that is attached to an air pump. As the balloon expands inside the mesh sleeve, the actuator contracts. The images above show the contraction of the pneumatic artificial muscles.

3D printed
actuator

For the design of the forearm, we wanted two degrees of motion: up-down and right-left. In the left image above, the shapes in bold represent 3D printed bone structure and the other shapes represent actuators. The 'elbow' joint on the bottom is connected to the 'wrist' through a ball and socket joint to allow multiple directions of motion. The actuators work in pairs. When one is fully inflated or contracted the opposite actuator is fully extended or deflated. To achieve a neutral position both actuators are half inflated. To determine the length of the actuators and the diameter of the structures, we worked backwards from the fact that we wanted about 20 degrees of motion in each direction. The spreadsheet above shows the factors we considered in this design.
Section View
Wrist

Elbow

Full View
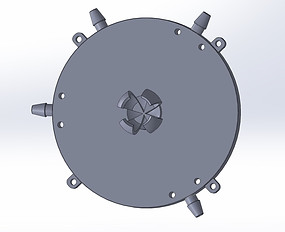
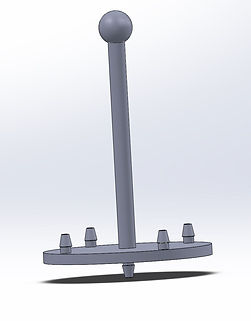
The CAD images above show the 3D printed bone structure of the forearm. The wrist is a modified version of the palm CAD above that was used as a proof of concept for the grabber/hand. In order to have the ball and socket joint in the center of the wrist, we had to move the input air channel to the side. Then we created a large hollow area inside the wrist so the air could evenly disperse to the three outputs that were connected to the fingers. The base of the elbow is very similar to the wrist. We have an input air channel at the bottom and four output air channels on the top. These output air channels connect to the pneumatic artificial muscle actuators. In the animation below, you can see a simulation of our forearm. The actuators in the simulation do not show how the pneumatic artificial muscles contract, but they give you a great idea of the way the forearm would move. I should note here that as this project was being completed in the spring 2020 semester, we were unable to finish physically prototyping the forearm as the semester moved online about halfway through, and the lab we were working in was closed.
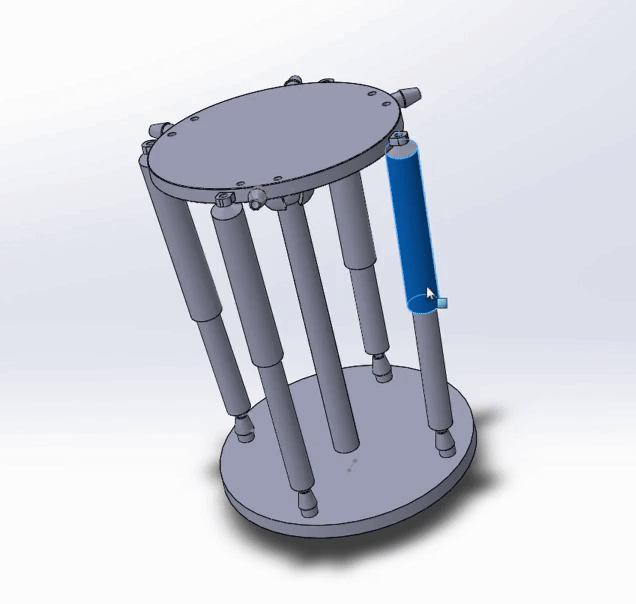